Verde Magnesium’s Ilhan Goknel authors for Spot Light Metal on magnesium extraction.
Magnesium metal is used in a diverse range of markets and applications exploiting the unique physical and mechanical properties of the element and its alloys. The use of magnesium increases annually as the lightweight properties are used to reduce weight, increase fuel efficiency, and reduce greenhouse emissions. But how is magnesium extracted?
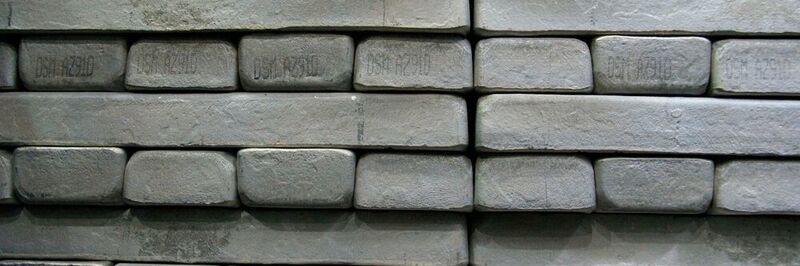
Magnesium Extraction: Horizontal Pidgeon Process
In 1941, Dr Pidgeon of Dominion Magnesium in Canada developed the Pidgeon process. Chemical reactions for the thermal process are relatively simple, including dolomite decomposition and magnesium oxide reduction. The dolomite decomposition or calcination involves and endothermic chemical reaction at an elevated temperature.
MgCO3.CaCO3 → MgO + CaO + 2CO2
Depending on the physical characteristics required for the dolime, the calcination temperature can vary from 780 to 1450 °C calcination conditions with influence the reduction reaction.
The calcined dolomite is then mixed with a reductant, typically silicon or aluminum, and heated at approximately 1150 to 1400 °C. At a low pressure of approximately 3 to 10 Pa magnesium oxide in the dolime reduced to metallic magnesium which escaped in the form of gas from the reaction zone and its captured at a reduced temperature.
2MgO + 2CaO + Si → 2Mg + CaO.SiO2
3MgO + 2CaO + 2 l →3Mg + 2CaO.l2O3
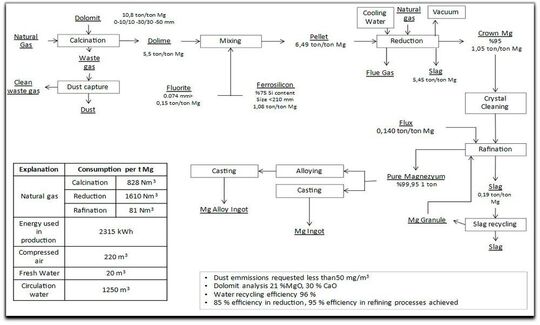
The reduction of alkaline earth oxides by means of silicon proceeds theoretically according to the equation:
2MO(S) + Si(s) = SiO2(s) + 2M(g) (I)
The reaction is reversible. Generally, it proceeds from right to left at allowing temperatures with the emission of heat and from left to right only at high temperatures with the absorption of heat. However, this simple equation is not followed, and a secondary reaction always occurs in which the resulting silica combines with a certain amount of unreacted alkaline earth oxide, forming silicate. Hence, when a theoretical reaction mixture is used according to the reaction as described above, only 1 mole of oxide is reduced from 2 moles of metal oxide and 1 mole of silicon and 1 mole of metal is formed and ½ mole silicon remains unused. For a complete utilization of the reducing agent, it is necessary to have twice the amount of oxide shown in equation:
4MO(s) + Si(s) = 2MO.SiO2(s) + 2M(g) (II)
In general, the reaction cases when a dibasic silicate 2MO.SiO2 has been formed. It has shown that in a system of alkaline earth oxide-silica, the dibasic silicate is preferably formed. Consequently, in the case of MgO, the reaction follows equation (II) where Mg replaces M. This alkaline earth oxide reduction method by reducing agents produces a volatile metal and non-volatile oxide known as early 1878.
Thermal reduction process proceeds as follows:
- 1. Calcination of dolomite to dolime,
- 2. Blending of the dolime with a reductant, such as ferrosilicon,
- 3. Heating of the dolime-reductant mixture is a vessel under vacuum,
- 4. Condensation of the liberated magnesium vapor,
- 5. Melting, alloying and casting of the condensed magnesium.
Magnesium Extraction: Vertical Pidgeon Process
The Vertical Pidgeon Process is a relatively new technology, with many advantages over the Horizontal Pidgeon Process. Several institutes in China have taken the vertical process into an industrial scale. With this method the retort is mounted into the furnace in a vertical position, load and unload of the material functions automatically by gravity, equipped with a matched machine, taking modernize control technology to monitor the material turning into raw magnesium and unload the slag. Meantime, it uses the slag’s waste heat to preheat the material; the vertical process is considered environmentally friendly with high heat application rate, which also ensures the automation, mechanization, and reduced labor intensiveness of magnesium production.
Compared with the traditional horizontal process, the vertical process has the following advantages:
- The production capacity for unit retort increases from 25 – 30 kg per retort to 65-70 kg. The vertical retort has a good result by heating, and all materials are evenly enriched in the retort. The temperature field in the retort is uniformly distributed, which is conducive to the reduction process, and it could be appropriately expanded to retort volume.
- The auxiliary production cycle is shortened by min. 1 hour per cycle, which is a total of min. 600 hours per year. This means an increase of approx. 8 % in capacity and energy efficiency, consequently.
- The gravity work has upper feeding and bottom slagging, equipped with appropriate equipment to realize the slag discharge and raw magnesium for mechanical transfer. It automatically discharges the slag, broke vacuum, open retort, and takes magnesium mold by modern control technology, which can greatly shorten the auxiliary production period and reduce workforce needs.
- The Vertical Pidgeon Process improves the service life of reduction retort. The time of charging and slagging is shortened, and the material is preheated. The phenomenon of sharp rise and fall of tank temperature is alleviated, and the service life of reduction retort is improved. By improving the alloy composition of the retort, minimum maintenance can be achieved. As a result, an additional workshop for recycling the retorts can be replaced by contracting third parties for recycling.
- Material load, slag unload, raw magnesium taken out could be done by machinery equipment and gravity; thus, the labor intensity could be reduced.
:quality(80)/images.vogel.de/vogelonline/bdb/1646700/1646713/original.jpg)
Basic Knowledge – Magnesium Alloys
Magnesium Extraction: Aluminothermic Reduction
The new process of dolomite clean magnesium smelting has two parts. The first is a new process for the comprehensive utilization of calcium and magnesium separation of dolomite. This process produces magnesium carbonate, which is a raw material of magnesium smelting. This stage solves the problem that the Pigeon method reduction slag cannot be comprehensively utilized. The second is the use of aluminothermic reduction, a new magnesium smelting process, which solves the waste gas residue of traditional magnesium smelting and uses the most advanced microwave heating technology today.
Part 1: New Technology of Comprehensive Utilization of Calcium and Magnesium Separation of Dolomite
New process of this plant layout was optimized based on the secondary pressurized carbonization method. First, the dolomite calcination equipment was improved, and then the subsequent process conditions were optimized and improved, and the secondary pressurized carbon chemical section was eliminated. To simplify, the carbonization efficiency is greatly improved, and the product quality is better. At the same time, the whole process has fully realized a new clean production process without waste gas, waste residue and wastewater discharge.
:quality(80)/images.vogel.de/vogelonline/bdb/1659300/1659360/original.jpg)
Magnesium Semisolid Casting
Part 2: New Technology of Thermite Reduction Magnesium Smelting
Thermite reduction method: The principle of magnesium production technology, under vacuum conditions, using metallic aluminum as a reducing agent to reduce magnesium oxide to prepare metallic magnesium, and by-product magnesium aluminum spinel. The preparation process includes a raw material mixing process and vacuum smelting process.
Compared with the Pigeon method, the total amount of reduction materials in this technology is reduced by more than 50 %. Energy consumption is reduced by about 54 %, and CO2 tail gas emissions are close to zero; spinel powder as a by-product can be sold as a product, and no waste residue is generated. The process is fully in line with the requirements of high efficiency, energy saving, clean and environmental protection.
Magnesium Extraction: Conclusion
For the last two decades, world production of magnesium metal has enjoyed a period of strong growth, despite a few interruptions. Since 2002, total global primary and secondary production has increased from an estimated 630 kt to slightly over 1.1 Mt or a cumulative annual growth rate (CAGR) of 5%. Recent primary production increases have taken place almost exclusively in China, with output declining or ceasing in several Western countries.
The cost of raw materials, energy, and labor within China is also rising, so Chinese Pidgeon plants’ operating expenses increase, thus pushing the cost of Chinese magnesium production closer to those of plants elsewhere in the world.
:quality(80)/images.vogel.de/vogelonline/bdb/1698100/1698154/original.jpg)
Material Safety
According to the Chinese government’s 12th Five-Year Plan, the Chinese magnesium industry’s targets are developing production, energy-saving and emission reduction, and more input in technological innovation and structural adjustment.
Due to significant capital costs involved, new electrolytic plant capacity is likely to remain minimal. Construction of new thermal plant capacity is more likely, achieved either through Pidgeon or alternative process production plants or by innovations in feedstock production methods for an optimized Pidgeon process plant.
Leave a Reply
Want to join the discussion?Feel free to contribute!